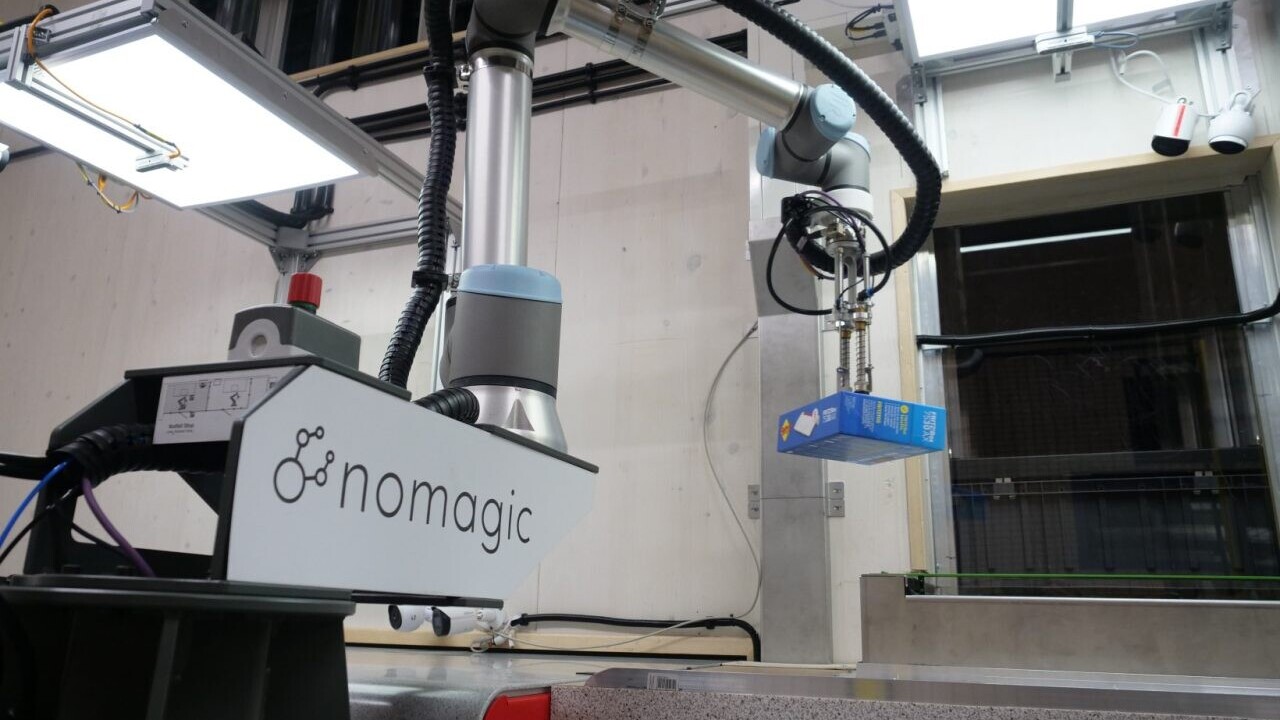
The robot arms train every night. About half a dozen of them, flexing in silence. They practise picking up items thousands of times over, to test whether their latest algorithms are working as intended. And in the morning, Nomagic’s engineers turn up for work to check how the machines did.
“This is a never-ending effort,” says co-founder and chief of strategy Tristan d’Orgeval. If the robot arms performed as intended, the updated algorithms get uploaded to the Warsaw-headquartered company’s live system.
Nomagic currently has 70 employees and has raised $39 million to date. Right now, dozens of the firm’s robot arms are toiling away in warehouses scattered around Europe. They pick and move an astounding variety of items — from t-shirts to bags of screws. They lift them out of storage bins; they sort them; they drop them into boxes for shipping.
The total number of these picking arms being used by various clients including fashion retailer ASOS and logistics company FIEGE is currently below 100 — d’Orgeval declines to reveal the exact figure. “We’re growing fast,” he adds, however, suggesting that the number of machines deployed commercially could triple over the next six months.
In the battle to ship goods as quickly and as efficiently as possible, retailers and logistics firms around the continent are increasingly turning to AI and robotics. These technologies promise streamlined sorting and shipping of individual items and yet they remain imperfect — sometimes robots pick the wrong item, or go the wrong way as they move around a warehouse.
Plus, adoption of these machines could limit the number of warehouse jobs that are available for humans in the future. The industry is nonetheless adamant that there is significant demand for automation.
Take your (robot) pick
Nomagic’s robot arms are tasked with picking and sorting foil-wrapped garments, glass jars, cardboard boxes and other items. Sometimes there’s no wrapping at all. It’s only when the arms can pick 95% or more of the items in a given warehouse that the company brings significant value to customers, says d’Orgeval.
And for those 95% of items, the arms should hardly ever slip up: “It needs to work more than 99.9% of the time.”

Nomagic’s robot arms have cameras mounted on them so that they can see and analyse what they are about to pick. They can lift anything up to about 5kg in weight and the machines can also decide, automatically, which tool to use for grasping a given item.
That choice will depend on the item’s size, shape, and material. A small suction cup might work for a smooth, flat, plastic-packaged item whereas a gripping finger or pincer-like blades would suit something less rigid, such as a soft packet containing textiles.
Human supervision
But what happens if the robot correctly picks up a package that happens to have been left open? How will it respond when the pair of shorts falls out unexpectedly? These sort of hiccups, which are not the robot’s fault, can still cause challenges, says d’Orgeval.
Nomagic has a team of operators that watch the bots in action and, if something does go awry, these human supervisors can connect remotely and fix problems on the fly. Occasional stumbles aside, the robot arms currently in production are performing well, says d’Orgeval, each picking an average of 650 items per hour. “A successful pick is probably three seconds,” he adds.
Humans might not always be as fast as that but millions of years of evolution has helped human hands to become extraordinarily adept at gripping or lifting things, and moving them around. Why get a robot to do what humans can do so well?
“I think the worry that we see the most nowadays — and it’s definitely much higher since Covid — is actually warehouse managers not finding people to fill the jobs,” says d’Orgeval. One vision for the future might be robots assisting better-paid human employees in warehouses, he adds.
Lack of workers
The warehouse worker shortage is a genuine problem, says Mehmet Dogar at the University of Leeds, who studies robotic manipulation of objects. Dogar is also currently working on projects partnering with Amazon and a logistics firm.
He stresses that robots must be able to coexist safely with human beings in warehouse environments, however. Last year, a man in South Korea was killed when a warehouse robot crushed him against a conveyor belt by mistake. D’Orgeval says Nomagic’s robots have never been involved in a safety incident. They operate within cages that prevent anyone from approaching the machine.
It may seem inevitable that AI and robots will come to dominate warehouses in the future though the pace and nature of the rollout will undoubtedly matter to people. As David Spencer, Dogar’s colleague at the University of Leeds noted in a blog post, “If workers and society rather than big tech companies […] are to benefit from automation, they need to have a larger influence and stake in it.”
Plus, robots, generally, are still limited in terms of function, argues Dogar. They can’t slide a hand into a random box to move unexpected inner packing material aside and see what’s in there in less than a second, as humans can, he notes: “We need to focus on more, and varied, skills — that is the biggest challenge.”
He says that, besides manipulation, the other task that startups tend to focus on for warehouse robot applications is navigation. For instance, how to get to one side of the warehouse, pick up a box, and bring it to the other side without getting lost or bumping into anything.
An unusual approach to this is currently under development at Opteran, a UK startup developing AI algorithms inspired by the way animal brains function.
‘A bit of bee’
“We take different things from different animals,” says David Rajan, CEO and co-founder. “We’ve got a bit of bee, a bit of fly, bit of ant, bit of rat.”
The company studies neural activity in, for example, insect brains while those insects navigate through experimental environments. And the patterns of their neural activity then influence how Opteran’s human engineers write their algorithms, as they aim to produce equivalent behaviour in a robot.
“Such a bioinspired approach may be promising,” says Dogar.
Earlier this year, Opteran announced a partnership with German logistics technology company SAFELOG, to provide software for its automated guided vehicles (AGVs) — squat, rectangular warehouse bots that slide under pallets to lift them up and carry them to a particular destination in a warehouse.

Among the benefits Opteran says its bioinspired algorithms offer is a high level of robustness. Harsh lighting or unexpected lighting changes inside the warehouse won’t trouble these machines, he insists. They respond to it dynamically. This, Opteran says, is a result of studying how animals deftly navigate to a goal, even while lighting changes around them.
‘People don’t lose jobs, things just evolve’
For SAFELOG, Opteran is providing part of the software it uses in its AGVs. Specifically, localisation and mapping. It will offer collision avoidance algorithms next year.
As for the risk to human jobs from the rise of warehouse robots, Rajan says, “The Luddites thought that about spinning,” referring to a group of craftspeople in the late 18th and early 19th Centuries in Britain who protested violently against the increasing mechanisation of their industry, in an attempt to protect their livelihoods.
“People don’t lose their jobs, things just evolve. Jobs change, […] new jobs are created, new roles, new opportunities,” adds Rajan, before going on to argue that the current adoption of automation in logistics is largely to do with addressing contemporary labour shortages and helping people to run systems inside large-scale infrastructure.
Research suggests that warehouse workers’ opinions about automation are mixed. While some fear job losses and potential mechanical failures, others praise improved efficiencies and point out that, in some cases, working alongside robots has improved safety.
Exactly how automation is rolled out, and integrated with an existing workforce, seems to be key as to whether it is, ultimately, perceived as either good or bad.
Get the TNW newsletter
Get the most important tech news in your inbox each week.