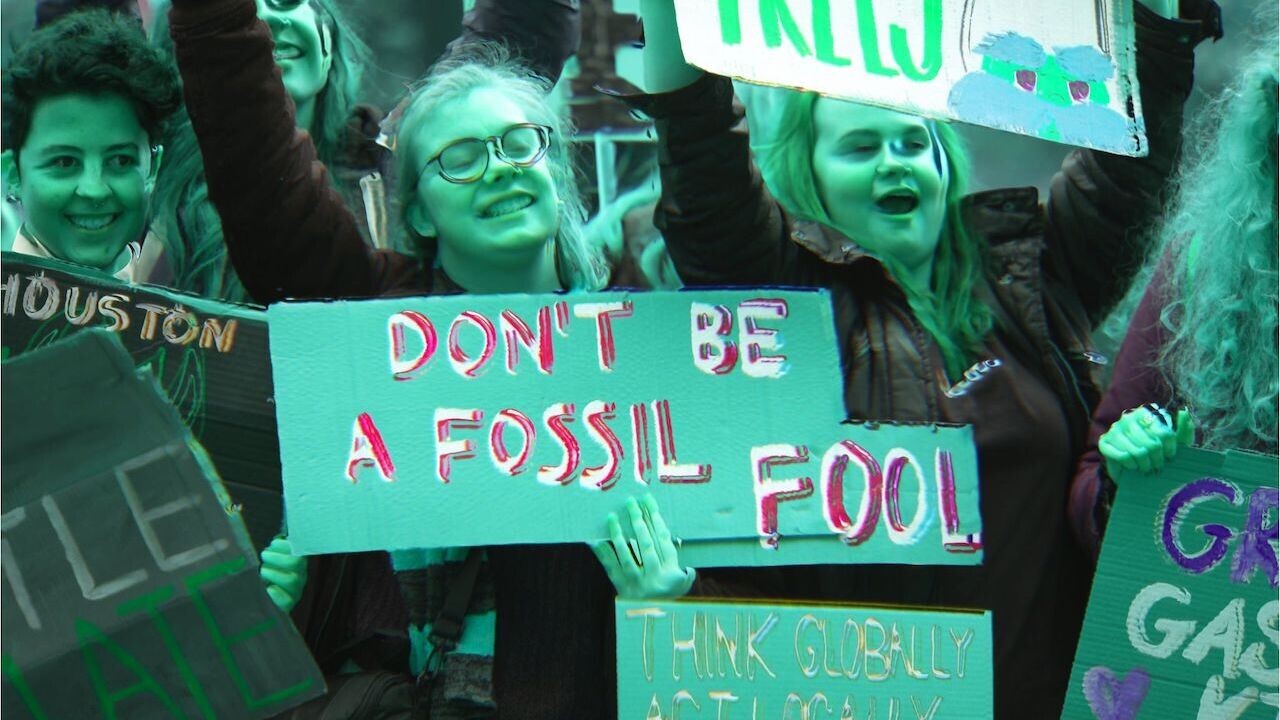
One of the major selling points of the electric vehicle is its oil-free, eco-friendly technology, which has been touted as a key solution to The Great Carbon Emissions Dilemma. But as EVs become increasingly mainstream, an important question has emerged among enthusiasts and skeptics alike: Are EVs truly the ‘greener’ option?
When it comes to getting around, experts broadly agree that plug-in cars are a more sustainable choice than traditional vehicles. However, as research shows, it gets a bit tricky at the manufacturing stage. A report from the MIT Energy Initiative reveals that during the production of EV batteries and other components, the emissions created are greater in comparison to the production of a gasoline-powered vehicle, and this poses a higher risk to the environment.
The good news is that most EV drivers can rest easy knowing that these high environmental costs are usually offset by the impressive energy efficiency of their vehicles over time. But as manufacturers create more processing plants and facilities to meet the rising demand for EVs across the world, it’s now more important to promote sustainable strategies that cause less emissions during production.
Here, we’ll examine the environmental concerns about EV manufacturing and what EV companies should be doing to address them.
The EV paradox: Using up energy to save energy
The most essential component of the EV is the lithium-ion rechargeable battery, which is popular for its excellent charging capabilities and ability to store up a lot of energy within a small space. These benefits do not come cheap, as the battery is manufactured from raw materials such as cobalt, graphite, lithium and manganese — minerals which are extracted and processed with high energy from carbon-emitting fossil fuels.
Material emissions will rise to more than 60% by 2040.
What this means, according to raw materials expert Minviro, is that for every tonne of mined lithium, 15 tonnes of carbon are emitted into the atmosphere. As battery research charges on, manufacturers are turning to more advanced materials like aluminum and nickel to create lightweight batteries that can take cars further. Since these minerals are also energy-intensive to mine and produce, they generate even more greenhouse gasses.
The battery is just one part of an EV — other metals used on the vehicle’s body and chassis go on to account for more than 47% of its manufacturing carbon footprint, according to a Greenpeace report. Despite this, the scale of production in EV megafactories, as well as supply chain activities, also add to the huge eco-footprint left behind at the end of the manufacturing process.
As the EV hype continues to take up more space and attract motorists, it only means more cars are going to be produced, which would in turn lead to further emissions. Take it from McKinsey & Co., which reports that material emissions are going to rise to more than 60% by 2040 from 18% today.
Make no mistake — the EV still remains a viable means to curb emissions from car transport. However, it’s now up to manufacturing companies to address the environmental damage done during the course of production. What measures can they take to improve their track record?
Capture raw materials, but make it ethical
Much of the world’s battery-grade lithium is sourced from mineral ore mines and liquid brine reservoirs beneath salt flats. The current methods used to capture these raw materials are highly energy-consuming, but there are alternative processes currently underway to control the environmental impact.
Direct lithium extraction (DLE) technology is one such process involving the use of techniques such as nanofiltration or ion-exchange resins. They act as a chemical sieve to collect the lithium chloride from brine reservoirs alone, leaving other salts in the water. The lithium chloride is then purified and concentrated to produce lithium hydroxide, which is used to make EV batteries.
Other smaller scale practices like extraction from geothermal water can also be helpful. Here, the lithium processing plants refine both high-grade lithium and clean water, which can be returned to the main source and reused.
To meet consumers’ sustainability demands, companies like Polestar are taking steps to keep the public informed about its sourcing of raw materials. The company maintains a continued partnership with software company Circulor, which now includes blockchain traceability of mica, in addition to cobalt that is already traced in the Polestar 2 batteries, from material source to finished product.
Sustainable factories make sustainable cars
Sustainable industrial design can help boost the energy efficiency during production, storage, and distribution of EVs. Energy-efficient models such as net-zero structures, can help conserve energy by utilizing high-performance envelopes, sunlight control, shading systems, and air barrier devices.
The amount of carbon produced during the manufacturing process should also be considered. One way to control the environmental impact is by installing premium efficiency motors and variable speed drives. This will not only help minimize energy consumption but also optimize efficiency in the production process.
While constructing an industrial warehouse or production facility, it’s important to consider renewable power sources as a major part of sustainable building design. Green technology such as solar panels can help manufacturers optimize power production and shrink their carbon footprint.
Polestar reduced greenhouse gas emissions by 6% per car sold in 2021.
Many energy-efficient buildings are also optimized for space, with optimal seals that control electricity waste and modernized lighting systems to decrease their reliance on the grid. While designing manufacturing centers, it’s worth taking care to increase the building’s compatibility with efficient devices to help reduce emissions from light and heat.
Making old batteries new again
Like every other industry concerned with mass production, the keyword here is ‘recycle.’
As the demand for EVs rises steadily and some of the existing models reach the end of their allotted life span, the need to repurpose old batteries for the production of new ones will become more pertinent. While this process is already in development, it’s important for manufacturers to roll it out on an industrial scale and play their part to support recycling. This would undoubtedly deliver further efficiencies for the EV industry.
Demystifying EV production
It’s still quite uncommon to hear EV companies discuss the scale of their manufacturing emissions, and the steps they’re taking to mitigate this. At the risk of losing the battle with emissions targets, it’s become important for businesses in the EV industry to expressly disclose the environmental impact of their operations.
In a recent report, Polestar announced that it was able to reduce greenhouse gas emissions by 6% per car sold in 2021, thanks to increased efficiency and use of renewable energy. The report also emphasized the company’s plan to create a truly climate-neutral car by 2030, to halve carbon per sold car between 2020 to 2030, and reach ultimate neutrality by 2040.
There’s no doubt that these measures will take time and require new innovations to help businesses move forward, but as Polestar shows, it’s important for EV manufacturers to provide honest, transparent reporting on manufacturing and production emissions to ensure they continue progressing in this area.
Get the TNW newsletter
Get the most important tech news in your inbox each week.